高炉炼铁、电炉炼钢
日期:2016-09-09 / 人气:2887
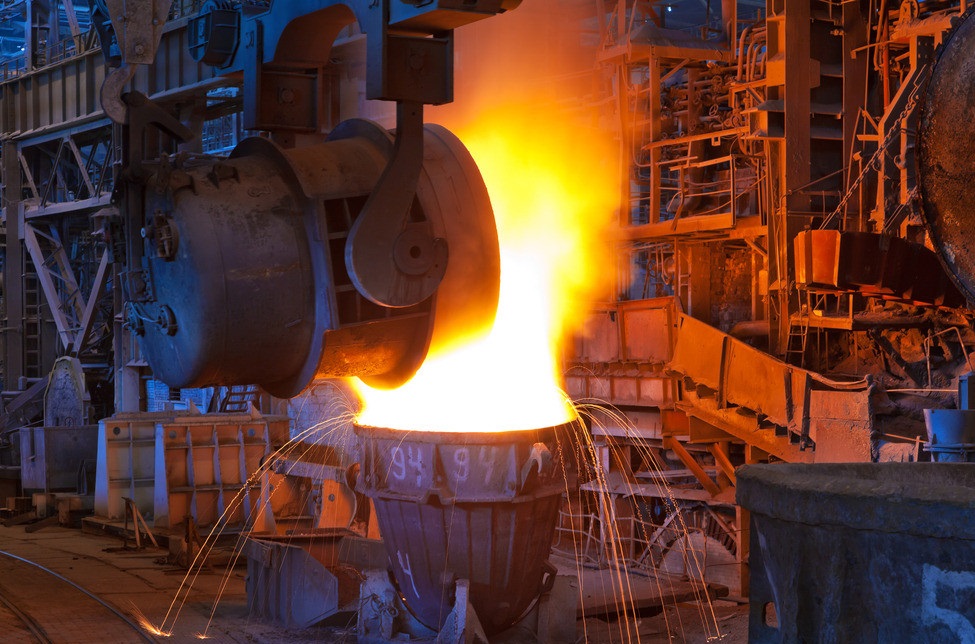
吹氧炼钢: 吹氧炼钢已为各国普遍采用,成为钢铁工业飞跃发展的一条重要途径。 吹氧炼钢的主要方式有:转炉纯氧顶吹或底吹炼钢、 电孤炉炼钢和平炉炼钢。转炉炼钢每吨钢耗氧50~60m3 ;电孤炉炼钢每吨钢耗氧10~25m3 ;平炉炼钢每吨钢耗耗氧 20~40m3 。电炉用氧可以加速炉料的熔化及杂质的氧化,这意味着电炉吹氧既可以提高生产能力又能够提高质量,电炉每吨钢耗氧量依照炼钢品种的不同而差异,所需氧气浓度为 90%~94%的富氧。中小型钢厂电弧炉炼用氧特点明显,用氧量不大,一般在1000~4000 Nm3 /h 左右,不需要氮气且间断用气。如采用深冷空分投资高运行费用大开停不方便。 变压吸附制氧工艺满足电炉炼钢需要,且投资见效快操作便。目前,国内厂家普遍采用,效益明显!
炼铁技术
㈠ 高炉炼铁
高炉富氧喷煤能够提高喷煤量,显著地降低焦比提高产量。更多的煤代替焦碳,节约的就是成本,只提高鼓风温度不可能达到目的。所需的富氧纯度只要求比空气含氧量多几个百分点,效果会很明显。如果深冷空分制取纯氧配比空气,比较浪费变压吸附制氧技术发展很快,大流量的富氧机正好合适,为这项技术的推广奠定了基础!
㈡ 熔融还原炼铁
熔融还原炼铁: 21世纪,对钢铁工业发展的基本要求是消除环境污染。为根本改变 钢 铁工业的污染现状,许多发达国家纷纷投入巨资开发熔融还原炼铁技术。熔融还原采用纯氧燃烧煤,代替焦炭炼铁。同时,产生大量高热值洁净煤气,作为 能源输出。它是一种发展中的新炼铁技术,其目的是以煤代焦和直接用粉矿炼铁,既无炼焦又无烧结使炼铁流程简化。受到许多国家的重视。熔融还原的目的是取代高炉。目前熔融还原流程多采用二步法,即先在竖炉(块矿)或流化床(粉矿)内将矿石进行预还原,然后 再 进入终还原炉。向终还原炉内加入煤和氧气,煤燃烧产生热和H 2 、CO等还原性气体,将经过预还原流程的矿熔化和进一步还原生成铁水和炉渣,H 2 和CO则供还原炉作为还原剂。和高炉流程相比,熔融还原的第一个特点是用煤不用焦可以不建焦炉;第二,多数用氧 而 不用风。目前唯一已工业化生产的熔融还原工艺是Corex流程。近代高炉已有数百年历史,其工艺已达到相当完善的地步。但在日益完善和大型化的同时,也带来了流程长、投资大以及污染环境等问题。随着世界上废钢铁积累日 益减 少,电炉流程迅速发展,这就要求采用直接还原新工艺生产出的海绵铁供电炉炼钢。 此外,由于炼焦煤资源日渐短缺,焦炉逐渐老化以及人们对焦炉污染日益关注,八十年代以 来,各发达国家纷纷谋求开发另外的无焦炼铁工艺——熔融还原. 其中Corex流程已 实现工业化生产。综合来看,当前炼铁工艺正朝着少焦或无焦炼铁方向发展,而直接还原与熔融还原技术正适合这样发展方向。所以我国应适度发展直接还原与熔融还原技术。